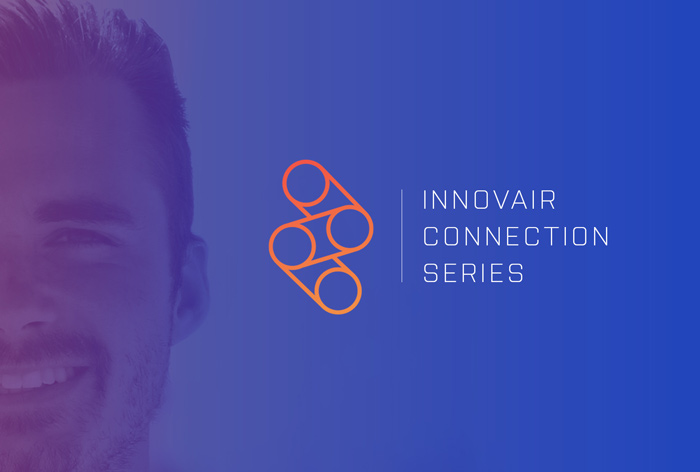
When it comes to industrial welding fume management, there are nearly as many different approaches as there are shops that use them. Since each company is unique in its systems, consumables, capacity, equipment and space, there’s no such thing as a one-size-fits-all fume management solution. However, there are some best practices that can help businesses maximize efficiency and productivity while boosting morale and reducing expenses.
We sat down with production and operation managers at two world class Manitoba-based manufacturing companies—K-Tec Earthmovers and Novid Inc.—to discuss their approaches to weld fume management and identify strategies that all businesses can learn from, regardless of size, sector or output.
It’s about more than air quality
The risks of poorly managed weld fume exhaust goes beyond the critical factors of employee health, safety, morale and sense of wellbeing. There can be significant production implications and risks to your bottom line as well. From broken machinery to workflow interruptions and soaring operating costs, fume management impacts all aspects of a company’s wellbeing.
And while it goes without saying that PPE (personal protective equipment) should be the last resort for welding fume control, too many shops use this as the first line of defense in lieu of effective welding fume extractors. The result is overly encumbered employees who work more slowly, get fatigued more easily and are at a higher risk than if the problem was addressed at the source. The business outcome? Reduced productivity and a detriment to your bottom line.
Manitoba success stories
Novid Inc. is a North American leader in the manufacture of stainless steel agri-products, including liquid fertilizer tanks, hopper bins and composting systems. They first approached Innovair Group for weld fume management support in 2019, seeking a more efficient and effective fume management system.
“Initially, we were just looking to increase the size of our machine,” says Riley Penner, Production Manager at Novid. “Our old system would get overloaded and we’d have to open the garage doors to let fumes out, which in minus-40 degrees celsius can slow things down a lot. But Innovair Group brought in an air quality specialist who conducted a welding fume analysis and came up with a fume extraction plan that worked with our shop.”
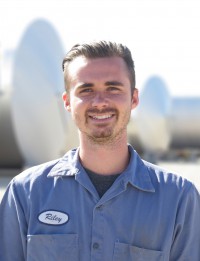
Riley Penner, Production Manager, Novid Inc.
While they maintain the use of PAPR systems for added safety, Penner says that the improved mobility and air quality resulting from the switch to a point of use extraction system has paid dividends.
“Instead of simply venting the fumes outside, the extraction system actually cleans the air so we can recirculate it back into the shop, saving on heating costs,” Penner says. “Our employees are healthier, happier and more productive, and they aren’t going through PPE equipment so much, which saves on cost. It’s also much easier and faster to clean our shop, which used to eat up time. The result is that we’re saving time and expenses while our throughput has gone up.”
Neil Blatz, Manager of Operations at K-Tec Earthmovers, has seen similar results from implementing new welding fume control efforts. K-Tec, which operates four shops run by a staff of 150 employees, manufactures industry-leading earth movers, scrapers and support equipment for commercial businesses across North America.
“When welding fume exhaust is poorly managed, more people get sick, morale is low, machines break and there’s always the possibility of the entire operation getting shut down,” Blatz says. “Innovair Group showed us ways to reduce smoke and fumes at the point of production, which included switching from metal core wire (which has a high manganese content and produces a lot of smoke) to a hard wire, and using equipment with a low fume pulse setting. The result is at least a 50 per cent reduction in smoke and fumes in the shop.”
Takeaways for business owners
Both Penner and Blatz say that business owners and operations managers looking to improve their welding fume exhaust systems should look for a supplier that takes their unique shop, capacities, equipment and space into account, and develops a custom plan to suit their needs.
“It’s important that we were able to see and try out all the different equipment options, including downdraft tables, extraction guns and wire types, so we could ensure we were maintaining the integrity of our operations and products while minimizing fumes,” Blatz says. “People working in all areas of operations have to try the equipment and feedback about what worked and what didn’t so we could find the best possible solution.”
Penner agrees. “Because they (Innovair Group) were able to take a look around the shop and learn about our specific needs and assets, they developed a plan for us that not only integrated with our existing systems and was cost-effective in the short-term, it also was built to scale-up and expand, to allow for our systems to grow.”
Blatz and Penner say that thorough consultation and trial up-front will help you ensure that your budget is well spent in the short-term and enables you to see cost savings down the line. And the benefits of improved staff safety extend well beyond a cheerful, healthy culture.
“The newer generations of workers especially take air quality and safety very seriously,” Blatz says. “When they see these systems in place, it shows that a business has taken a serious approach to ensuring staff are protected. It demonstrates that they care for their staff. This will help you hire good people and keep them around for longer.”
Visible results
Ultimately, welding fume control and extraction has greater benefits to a business than employee health (although that alone should be enough to motivate most company owners to meet emission standards). Extracting fumes at the source and mitigating reliance on PPE can help you improve productivity, staff attraction and retention and ultimately your bottom line, while reducing expenses and employee health risks.
The most important factor in implementing your new system is finding a partner who will collaborate closely with you to develop a plan that addresses your unique needs, space, equipment, processes and growth goals. Haphazard implementation of fume management techniques will ultimately lead to an incohesive, unreliable and costly system.
As new generations enter the workforce, they are looking for employers who demonstrate a clear understanding of workplace risks and place high value on employee health, safety and wellbeing. Attract and keep your best workers for longer by creating an environment that is clean, safe and easy to work in.